ISO(国際標準化機構)による品質マネジメントシステムISO9001-2008及び環境マネジメントシステムISO14001-2004の認証を取得し、維持・継続をしています。
少しでも技術レベルの向上を図るべく、自ら設定した技術課題に対して内部検討、実験を行ない、技術レポートとして集約、蓄積をしています。
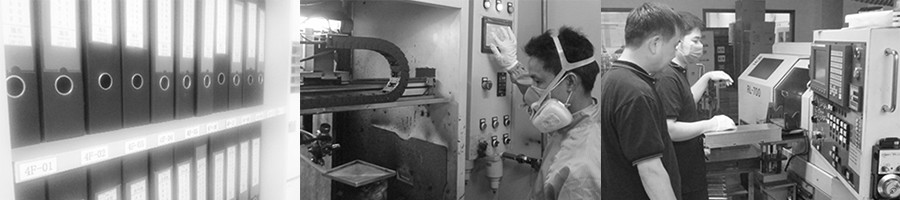
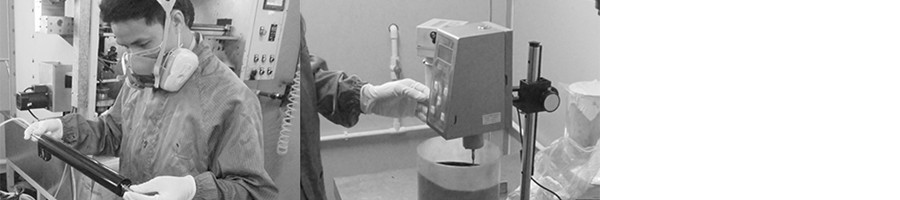
機械化による省力化(切削工程)
改善前 | 改善後 | |
---|---|---|
内容 | 加工前品の投入、加工後品の取り出しなどは作業員が手作業で行っていた。 | 自動ローダー装置を採用、製品の加工投入作業を自動化。 |
問題点と改善 | 作業効率が悪い。 作業者の安全性の問題あり。 |
1人で2台の外径機を操作可能にした。 手作業がなくなることで安全性が向上。 |
効果 | 1台の設備に1人の作業員が必要。 | 2台の設備を1人で操作可能、人区効果が2倍(半減)。 |
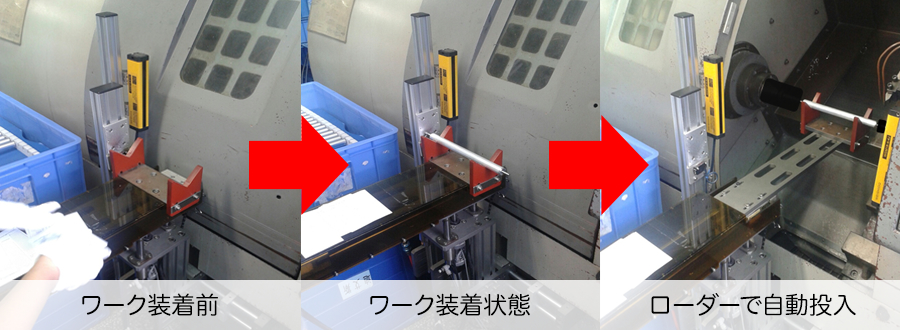
機械化による省力化(圧入工程)
改善前 | 改善後 | |
---|---|---|
内容 | パイプ、ピンを作業者が圧入機にセットし作業していた。 (半手作業) |
パイプとピンをそれぞれローダーに入れ、自動圧入を可能にした。 (自動作業) |
問題点と改善 | 1本作業毎に、パイプ、ピンをセットし直すという手作業があり工数がかかっていた。 | ローダーによる流れ作業が可能になり、1本当たりの圧入秒数短縮。 |
効果 | 1台の圧入機に常時作業者が作業していなければならなかった。 | 作業者が圧入機につきっきりでいる必要がなくなった。 人区削減および工程秒数短縮化 |
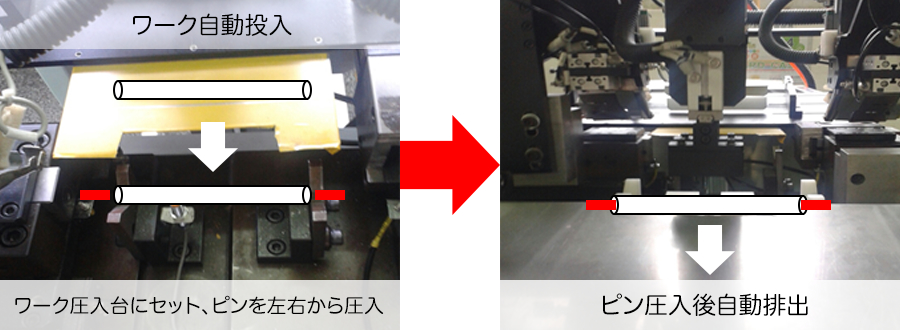
機械化による省力化(パーカー工程)
改善前 | 改善後 | |
---|---|---|
内容 | 各槽の処理時間や、槽間の移動作業など作業員がそれぞれ手作業で行っていた。 | 浸漬時間等をアラーム管理。各槽への移動はホイスト使用による自動化を実現。 |
問題点と改善 | 不適切な処理時間(超過)などのポカミスによる不良発生などあり。 | 処理時間等をセットして管理することでポカミス防止とホイストでの自動移動による効率化実現。 |
効果 | 品質バラツキ、不良率が下がらない。 | 品質の安定化と不良率低減。 |
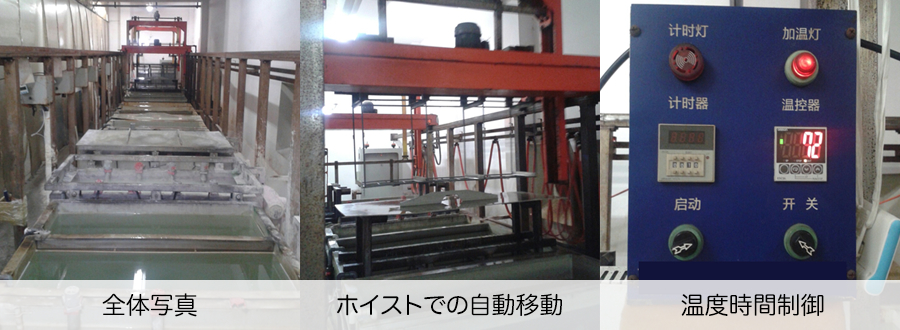
面粗さ精度向上 (Ry3.0→Ry1.0)
改善前 | 改善後 | |
---|---|---|
内容 | 既存設備での加工限界。 | 専用の表面粗さ加工設備導入。 |
問題点と改善 | 高精度の面粗さの対応が困難。 | 面粗さの加工精度改善/向上。 |
効果 | 一般的なアルミ製品の表面粗さ。 非鏡面Ra1.6以下 鏡面Ra0.4 / Ry1.6 |
Ra0.2 / Ry1.0以下 対応可能 |
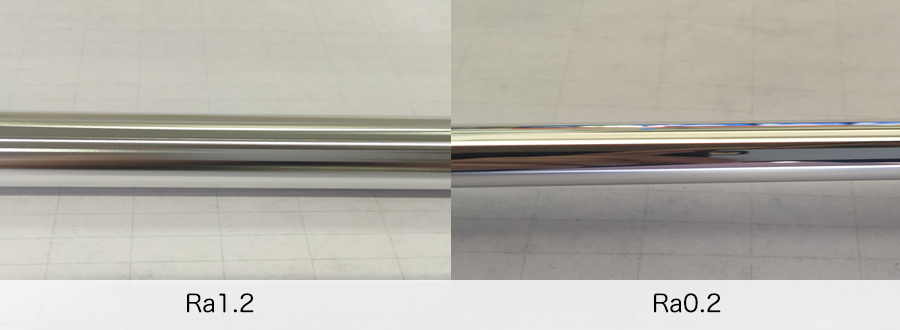
センタレス研磨回数削減
改善前 | 改善後 | |
---|---|---|
内容 | 従来は一般的な粗研磨工程の研磨回数で実施していた。 | 粗研磨工程の研磨量、条件見直しにより研磨回数を削減。 |
問題点と改善 | 研磨回数が多い=コスト高 1回あたり研磨量増やすと製品への加工負荷大。 |
研磨量、スピードの各種水準を試験、研磨回数の削減達成。 |
効果 | 粗研磨工数が減らないと加工費が下がらない、また製品が増えると加工設備が足りなくなる。 | 粗研磨工数の工数短縮実現による加工費の低減と加工設備のキャパシティーアップを実現。 |